With plusmeta to the Digital Data Chain

von Mischa Vollmann
Juli 14, 2022
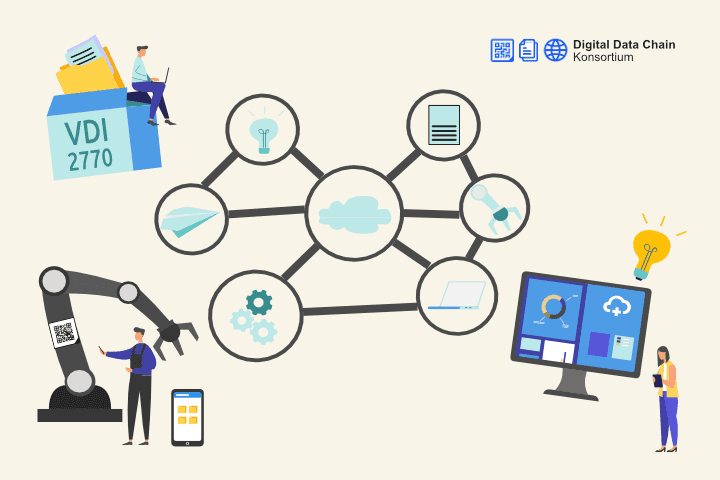
The Digital Data Chain • Grafik: plusmeta GmbH, Viktoria Kurpas/Shutterstock.com
Exactly the right information, at the right time, at the right place - indispensable for Industry 4.0. But to ensure this, it requires close cooperation between all parties involved: plant operators, service providers and manufacturers of machines and components are equally in demand.
Prerequisites for a smooth, digital exchange of information are a uniform access option, a common exchange format and a unique identification of plant components. Standards are ideal here because they create the necessary framework conditions. As part of the Digital Data Chain Consortium (DDCC), plusmeta supports this development. But what exactly does this body stand for?
The Digital Data Chain Consortium
In order to pave the way to Industry 4.0, plant operators, technology suppliers and service providers for plant operators, especially from the process industry, have joined forces in the Digital Data Chain Consortium. The goal: to jointly develop the three core technologies of
- Identification
- Standardisation and
- exchange
The development of common standards and systems will lay the foundation for the Digital Data Chain. Because everyone benefits from the optimised exchange of technical data and information.
Through the smooth exchange of project information, operating procedures and processes can be further automated and thus made more efficient. This strengthens competitiveness and saves valuable resources through less wear and tear and idle time.
As a member of the Digital Data Chain Consortium, plusmeta is actively involved in the developments. Our plusmeta platform provides the optimal interface between the various process participants and links them cleverly using artificial intelligence.
The three Digital Data Chain technologies in focus:
- The automatic and unique identification of physical objects
- Digital manufacturer information (VDI 2770)
- Digital information exchange platforms (IEP - Information Exchange Platform)
Automatic identification of physical objects
The basis for the unambiguous recognition and assignment of components is the IEC 61406 standard (formerly DIN SPEC 91406), also frequently referred to as “AutoID “.
In order to work efficiently and in a resource-saving manner during maintenance and repair work, all installed components are given a unique assignment. To achieve this, an internationally valid standard is required. To develop this, more than 30 companies from the process industry have joined forces in the Digital Data Chain Consortium to jointly develop a globally applicable standard.
This is how DIN SPEC 91406 finally became IEC 61406. This globally unique and machine-readable ID is affixed to the nameplate of the physical components and integrates them accordingly into the digital data chain. This ID is a URI (Uniform Resource Identifier) for which particularly specific rules apply. IEC 61406 describes these rules. For example, it specifies a character limit to suit the requirements of the respective systems that typically manage information of this type.
The ID can be represented in the form of a QR code and initially serves simply as a one-to-one identifier. Once the digital data chain has been fully implemented, the responsible technician can access further relevant information, such as maintenance plans or operating instructions, via an information exchange platform (IEP) after scanning.
Generate AutoID (IEC 61406) easily in plusmeta
The plusmeta platform offers automated functions to generate IDs according to the requirements of the standard - simple and user-friendly with the help of our intuitive workflows. In plusmeta, the ID can be composed of several metadata. It is important that there is at least one component that makes each individual physical object identifiable. Often this is the serial number. In the plusmeta platform, the appropriate QR code can also be generated directly, which can then later be applied to the corresponding component.
Security is also the top priority here: components of the AutoID can be encrypted if required. If the codes are created in different departments, at different points in the process, there is also the option of generating identical, encrypted IDs for identical products using common keys. Here, too, plusmeta provides support with comprehensive options for collaborative work.
Unique identification of physical objects • Graphics: plusmeta GmbH, Viktoria Kurpas/Shutterstock.com
Digital manufacturer information
VDI guideline 2770
The amount of technical documentation that belongs to a machine and its components is often large. Parts lists, assembly and maintenance instructions, test reports, certificates and circuit diagrams. In the past, this amount of data was stored in a wide variety of formats and structures. These are then passed on to plant manufacturers and operators in digital and sometimes also analogue form in paper form.
To standardize information regardless of manufacturer - With the VDI guideline 2770 “Digital manufacturer information for the process industry”, a universal standard was created here that clearly defines information: properties, structure, scope, content and data format now follow a uniform one Shape.
The use of PDF/A also ensures that the information will still be accessible many years from now. Combined with the use of metadata and the clear assignment to physical objects by IEC 61406, the information is therefore available to employees, technicians and workshops when they really need this information. Simple and fast, for maximum efficiency.
We have more information on the requirements of VDI 2770 in a blog series on the subject held.
Automation with plusmeta With the help of plusmeta, the creation of VDI 2770 packages, as an important part of the digital data chain, can be significantly simplified and (partially) automated. plusmeta’s intuitive workflows ensure that, in the end, valid and standard-compliant packages are created that meet the required requirements. A number of practical functions are integrated into plusmeta for this purpose, such as the PDF/A conformity check and an optional PDF/A conversion. Microsoft Office files can also be converted to PDFs directly in plusmeta.
With the help of artificial intelligence, plusmeta automatically recognizes the metadata required by VDI 2770 (e.g. document categories) and meaningfully links them to the corresponding documents. In addition, format variants (original formats such as Excel, DXF, etc. supplied with the required PDF/A documents) can be automatically linked and thus correctly output in the package.
After approval, standard-compliant VDI-2770 containers with the appropriate storage structure and XML metadata files can be generated at the push of a button.
With the help of interfaces to data sources, even fully automated processes for generating VDI 2770 packages can be implemented.
More information on creating VDI 2770 containers in plusmeta is in found on our blog.
Digital manufacturer information • Graphics: plusmeta GmbH, Viktoria Kurpas/Shutterstock.com
Cloud-based information exchange platforms
Using various IEP (Information Exchange Platforms), the corresponding manufacturer information can be easily provided and easily accessed by service providers and plant operators at any time.
Manufacturers, plant operators and service providers remain connected to each other over the entire product life cycle. Engineering and maintenance processes can be continuously optimized over the entire life cycle.
Integration of interfaces with plusmeta
plusmeta offers various options for the implementation and automation of corresponding interfaces. In a joint pilot project with Festo and SAP, an integrated data transfer from plusmeta to SAP AIN was successfully implemented.
With the resulting Workflow “Create Digital Twin for AIN”, it is now possible to create a digital twin, which is the perfect basis for networked work in the
Cloud-based information exchange platforms
Using various IEP (Information Exchange Platforms), the corresponding manufacturer information can be easily provided and easily accessed by service providers and plant operators at any time.
Manufacturers, plant operators and service providers remain connected to each other over the entire product life cycle. Engineering and maintenance processes can be continuously optimized over the entire life cycle.
Integration of interfaces with plusmeta
plusmeta offers various options for the implementation and automation of corresponding interfaces. In a joint pilot project with Festo and SAP, an integrated data transfer from plusmeta to SAP AIN was successfully implemented.
With the resulting Workflow “Create Digital Twin for AIN”, it is now possible to create a digital twin that offers the perfect basis for networked work in Industry 4.0.
The associated VDI 2770 containers are also transmitted and can be shared directly with other companies, such as the plant operator.
IEP – Information Exchange Platform • Graphics: plusmeta GmbH, Viktoria Kurpas/Shutterstock.com
Are you curious? Contact us and take your technical documentation to the next level. Write us an email to hallo@plusmeta.de!